In industrial settings, safety is paramount. Among the numerous safety protocols and systems, gas detection calibration stands out as a critical component. Ensuring the accurate detection of hazardous gases can prevent accidents, save lives, and maintain operational efficiency. This blog explores the vital role of gas detection calibration in industrial safety and its importance in maintaining a secure working environment.
Understanding Gas Detection Calibration
Gas detection calibration involves adjusting the readings of gas detectors to ensure they accurately reflect the concentrations of specific gases in the environment. Over time, gas detectors can drift from their original settings due to environmental conditions, sensor degradation, or other factors. Regular calibration ensures that these detectors remain reliable and accurate, providing a true representation of gas levels in the area.
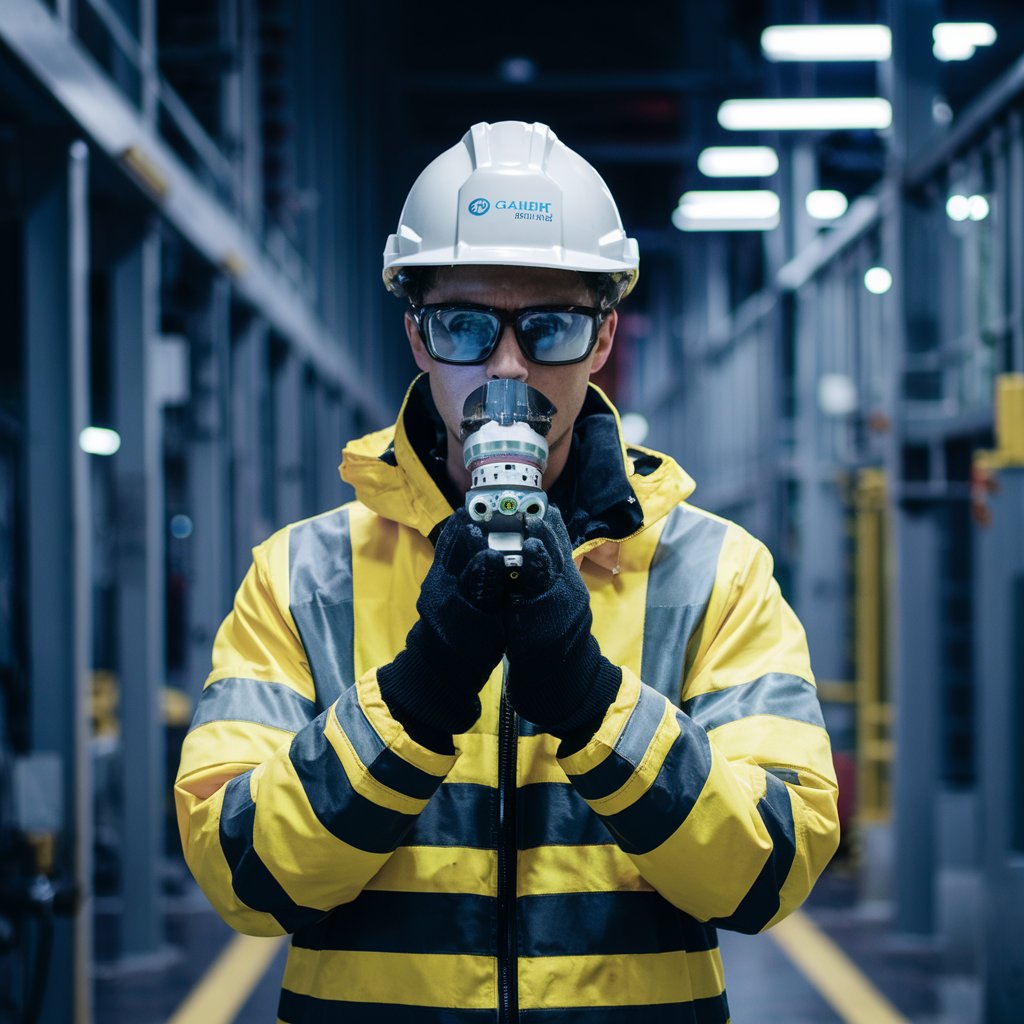
The Importance of Gas Detection Calibration
Ensuring Accurate Readings
- Preventing False Alarms: Uncalibrated detectors can lead to false alarms, causing unnecessary evacuations and disruptions. These false alarms can desensitize
- Avoiding Missed Detections: Conversely, detectors that are not calibrated correctly may fail to identify dangerous gas levels, putting workers at risk of exposure to toxic or explosive gases
Compliance with Regulations
- Regulatory bodies mandate regular calibration of gas detectors to ensure workplace safety. Compliance with these regulations is not only a legal requirement but also a moral obligation to protect employees.
- Failure to comply with these regulations can result in severe penalties, including fines, shutdowns, and legal liabilities
Protecting Workers’ Health
- Exposure to hazardous gases can cause serious health issues, ranging from respiratory problems to long-term chronic illnesses. Accurate gas detection is essential in preventing such exposures and safeguarding workers’ health.
- Regular calibration helps identify potential leaks or hazardous conditions before the pose a significant health risk.
Preventing Explosions and Fires
- Many industrial gases are flammable or explosive. Accurate gas detection is crucial in identifying leaks and preventing potential explosions or fires.
- Proper calibration ensures that the detectors can alert personnel to evacuate or take corrective action in time, thus preventing catastrophic incidents.
Steps in Gas Detection Calibration
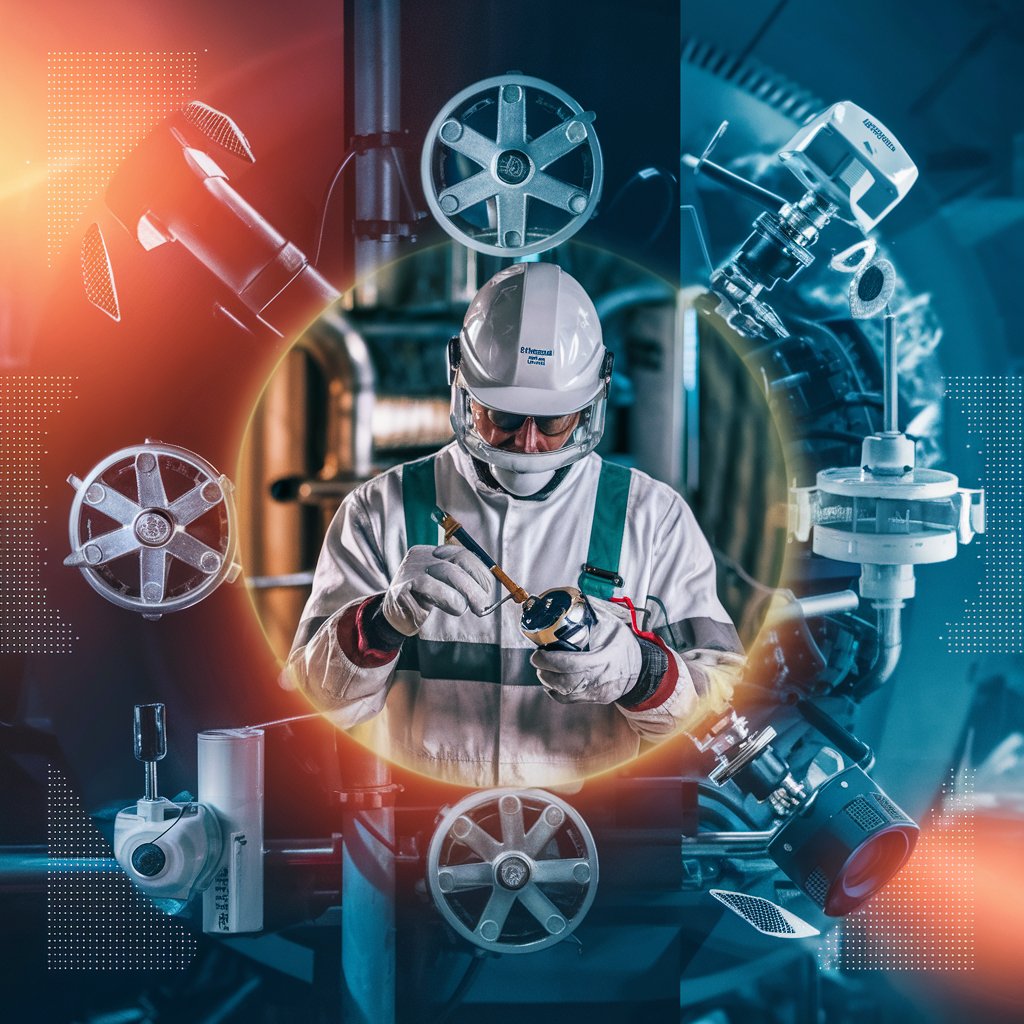
- Initial Testing
Before calibration, an initial test is conducted to check the current accuracy of the gas detector. This involves exposing the detector to a known concentration of gas and comparing the readings. - Adjusting the Detector
Based on the initial test results, adjustments are made to the detector’s settings to align its readings with the known gas concentration. This may involve software adjustments or manual calibration. - Verification
After calibration, the detector is tested again to ensure that the adjustments were successful and that the readings are accurate. This verification step is crucial to confirm the reliability of the detector. - Documentation
Calibration results are documented for record-keeping and compliance purposes. This documentation includes the date of calibration, the person who performed the calibration, and the results of the tests.
Best Practices for Gas Detection Calibration
- Regular Calibration Intervals
Establish a regular calibration schedule based on the manufacturer’s recommendations and industry standards. Regular intervals help maintain the accuracy and reliability of gas detectors - Qualified Personnel
Ensure that calibration is performed by qualified personnel who have the necessary training and expertise. Proper training is essential for accurate calibration and reliable results. - Use of Calibration Gas
Use certified calibration gases that have traceable standards to ensure accuracy. The concentration of the calibration gas should be appropriate for the detector being calibrated. - Environmental Considerations
Calibrate detectors in a controlled environment to prevent external factors from affecting the results. Temperature, humidity, and other environmental conditions can impact calibration accuracy.
Conclusion
Gas detection calibration is a cornerstone of industrial safety, ensuring that gas detectors provide accurate and reliable readings. By preventing false alarms, avoiding missed detections, complying with regulations, protecting workers’ health, and preventing explosions, regular calibration plays a critical role in maintaining a safe working environment. Adhering to best practices and establishing a rigorous calibration schedule can significantly enhance the safety and efficiency of industrial operations. Remember, when it comes to industrial safety, accuracy is non-negotiable.